At AUTOMOBILITAS Planning and Programming begins with operational needs assessments that includes documentation of important design assumptions, goals and project constraints. Our rigorous concept generation phase captures all potential opportunities for improvement and focuses on short and long-term project goals. Plans include detailed future state layouts, process descriptions and capital investment plans for ease of execution and project management.
Why choose this service
Our design approach – from operational layouts and sub-systems to full WMS and ERP design – tailors equipment, workflow and software to the organization for optimized efficiency and ROI. From our Systematic Layout Planning approach to a detailed specification and bid approach for vendor selection and monitoring, we measure and verify every aspect of a project through every step.
- Workflow Design and Process Improvement
- Facility Layout Planning
- Material Handling System Design
- Operating Process Documentation
- System and Software Requirements
- Equipment Specifications
- Lean Training Programs
- A / E Design Interface
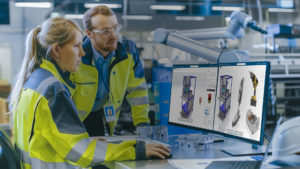
The process of factory layout planning
The first task of a factory planner is typically to fully understand the space in which manufacturing is to take place. Perhaps they’re already familiar with the location, but they want an update on the current conditions of the site.
This will include the dimensions of the space, the locations of any structures which already occupy it and needs to be accommodated in the factory design, such as pillars or columns or trusses supporting the roof, where power, water and other utilities may be brought into the site, and the access points for people and materials.
To accurately determine these vital points, indoor mapping technologies such as laser scanning to obtain point-cloud data may be used, and the results uploaded into the Computer-Aided Design (CAD) packages that will invariably be used to design the equipment layout.
Also important is to understand the product being manufactured, the complexity of which will determine what the factory layout ultimately looks like.
The production process must be broken down into its various stages and each must be understood on a detailed and technical level.
For example, if metal needs to be shaped into specific forms for carmaking, there are questions like:
+ Will this be done by bending sheets, grinding blocks, drilling holes, or a combination of all of these?
+ Will these tasks be accomplished using multi-functional machine tools or will people be using the appropriate tools to do them by hand?
+ When it comes to joining opponents together, will they be welded, glued or joined using mechanical means, such as rivets, screws or bolts?
+ Is a clean electrical connection required?
+ How accurate do all these operations need to be?
In each case, the appropriate space needs to be reserved for the machines or workbenches, the appropriate equipment selected and the necessary utilities brought to the location.